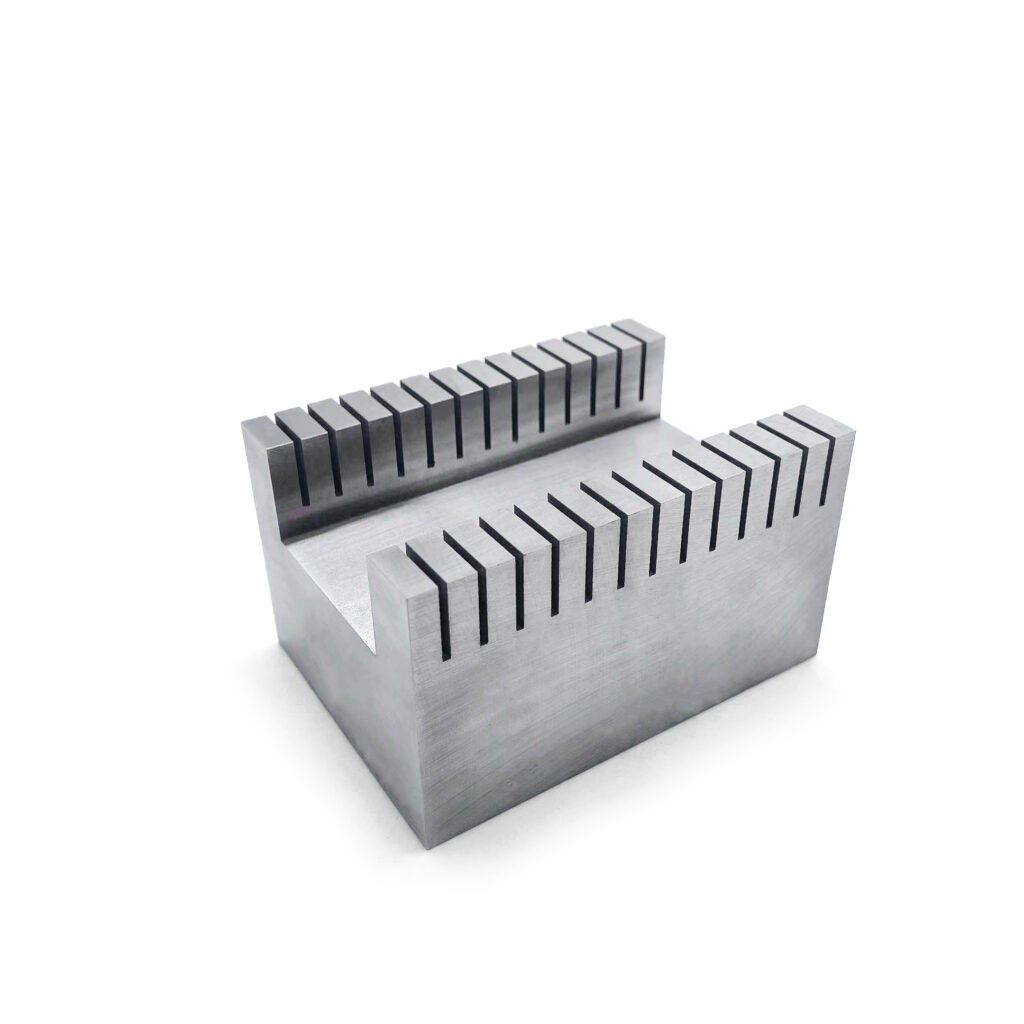
Cast AlNiCo Magnets
Cast AlNiCo magnets are made of liquid AlNiCo by melting an alloy of aluminum, nickel and cobalt at very high temperatures (1400-1500 degrees Celsius) and then under very high pressures (500-1000 tons per square centimeter), when it has cooled sufficiently, the resulting cast Alnico block can be drilled, sawed, ground or turned on a lathe according to specific requirements. Cast AlNiCo magnets usually require heat treatment to further improve their coercivity properties. Cast AlNiCo magnets are divided into isotropic and anisotropic forms according to the direction of application of the magnetic field to orient the magnet after heat treatment; if no magnetic field is applied during cooling, it can be classified as an isotropic material; Instead, if they were cooled with a magnetic field applied, it would become an anisotropic material.
Alnico magnet pdf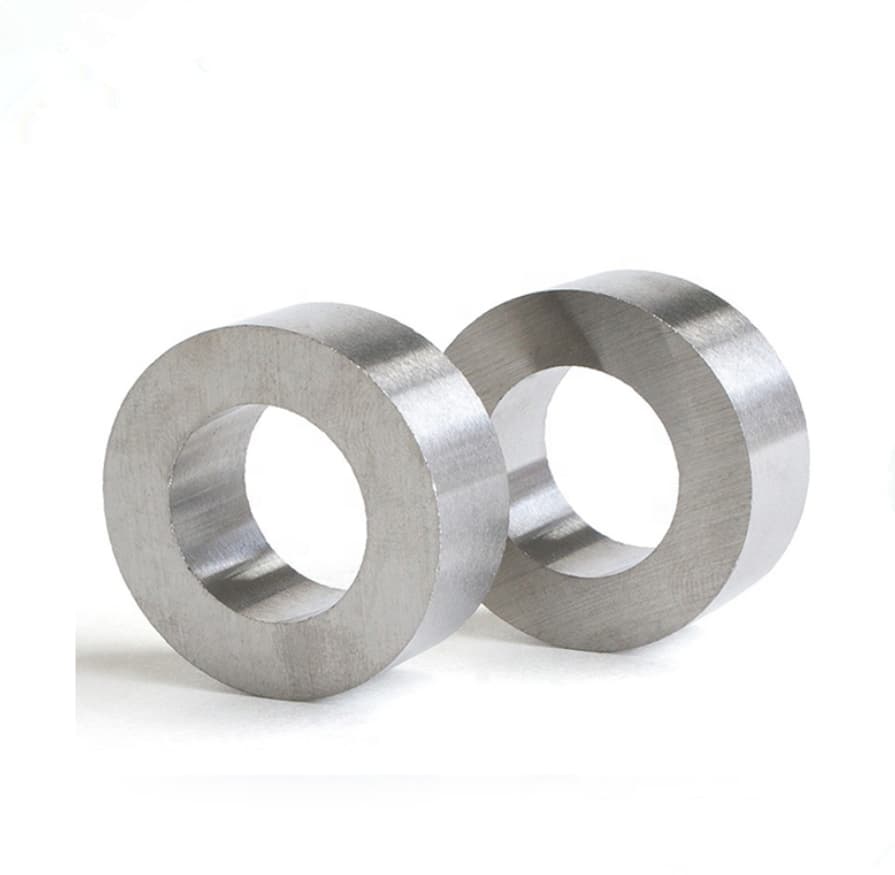